The Bottom Line:
- Automating operations can conserve snack and bakery labor
- Packaging robotics accommodate various sizes, formats, and counts
- Such technology can handle specialized handling and placement applications
Bakery and snack producers are creating a wide range of products to meet consumer demand; they also are being called on to do more with less. This has led many plant managers to automate packaging operations, which reduces labor costs. Manufacturers have responded by developing automated packaging systems that handle a variety of formats, sizes, and counts. Robotics is a big part of these innovations.
Producer perspectives
Kellogg's is a global food company with a history dating back to the late 1800s. Founded by W.K. Kellogg, the company has since grown into a major player in the food industry, producing a wide range of breakfast cereals, snacks, and bakery products.
Kellogg's uses packaging automation to create efficient production lines with the capacity for high throughput volume. This entails using automation in areas where manual labor may struggle to keep up with rapid rates of product output. “Our automation systems handle tasks such as placing products into containers and transporting them to the end of the line, as well as filling unit loads and loading them onto trucks via forklifts. The product mostly remains untouched by human hands until it reaches the retailer,” says David Sosnoski, director of packaging engineering for salty snacks, Kellogg Co.
Robotics plays a significant role within Kellogg’s packaging automation initiatives, offering a diverse range of options, from basic and simple robots to advanced collaborative robots (cobots). “Cobots are designed to replace repetitive human tasks that do not require a larger, fully automated solution,” Sosnoski says. “They have proven valuable in filling the middle ground between tasks that are too complex for traditional automation but exceed human capabilities in certain areas.”
Kellogg’s automated systems, particularly its computerized weighing systems, have been crucial to achieving its weight targets. This contributes to improved productivity and positively impacts the bottom line, especially for more expensive products such as Cheez-It. Automation also has helped address repetitive labor scenarios that may pose ergonomic challenges and hinder productivity. “By automating certain tasks, we have been able to reduce the chronic issues caused by repetitive motion, benefiting the well-being of our staff,” Sosnoski adds.
Mondelēz International is one of the largest snack companies and a major producer of cookies and crackers. The company is growing rapidly in the area of baked snacks as well. Its automated packaging systems start with the product feeding process, where items are seamlessly transferred to primary packaging machines, such as baggers or wrappers. Subsequently, the products progress through secondary and/or tertiary packaging stages, ultimately being packed into cartons by robotics systems.
Within its packaging systems, the company leverages robotic technology to execute a wide array of tasks, including tray loading, palletizing, case packing, bundle stacking, and slug pick and place. “Advanced robotics play a pivotal role in accelerating the packaging processes, leading to enhanced speed, efficiency, and an elevated standard of packaging quality and food safety,” says Min Ling Chan, senior director of global engineering digital, automation, and packaging at Mondelēz International.

Robotics ensure consistent packaging of finished goods with improved precision, minimizing the risk of errors and enhancing quality control at Mondelēz. “As a result, our packaging systems exhibit increased throughput, optimizing production rates and output. By streamlining packaging processes and incorporating robotics, our packaging systems not only boost efficiency and productivity but also contribute to a safer and more reliable production environment,” Chan adds.
Also, automating tasks that involve heavy lifting and repetitive motion reduces the risk of workplace injuries and operator fatigue. “The integration of safety features, such as sensors and safety design, ensures that packaging machinery operates safely, with automatic stops in case of any safety breach,” Chan says.
Unique Snacks is a family-owned and operated snack producer based in Reading, PA, known for its signature pretzels, including Original Splits, Pretzel Shells, Sourdough Craft Beer Pretzel Rings, Sprouted pretzels, Chocolate Coated Splits, and Peanut Butter Crunchies.
Unique Snacks is just starting to look at automated packaging equipment, with the first unit arriving by the end of 2023, according to Justin Spannuth, chief operating officer. “As we were doing research, we found that any upgrade comes with positives and negatives. The positives are obvious with the need for less people to achieve the same amount of output,” he says.
One negative is the fact that more automated equipment requires more mechanics, which is the most difficult skilled labor job to fill, Spannuth notes. “If you are able to dedicate a line to a single size package and reduce the need for changeovers, the fewer headaches you will have. Of course, the size of the company matters in making any decisions on adding automation. We will continue to look ahead at new packaging automation but it will need to make sense for our applications.”
Equipment insights
Cama North America manufactures a wide range of packaging solutions for the bakery sector including cartoners, case packers, tray packers and sleever machines. The company recently installed a cartoning and wraparound case packing system at a large bakery that produces goods presented in pie tins and sealed into bags that are twist-tied at the neck. Due to increased product demand, they were looking for an automated secondary packaging system to replace manual and semi-automatic operations.
Cama’s solution included its Model IF315 top-loading system with integrated robotic orientation, as well as robotic loading, cartoning and wraparound case packing functions within a Monoblock frame that also features a vision-guided RB590 Triaflex delta robot. The result: a smaller and less complicated Monoblock system that improves production.
“Cama’s packaging design team worked with the company to develop a tri-seal carton and a wraparound case, which provides identical aesthetics and shelf-ready tear offs, but can be formed and fed from a blank magazine, in a process that is less costly for the materials, less complicated to operate and takes up a smaller footprint,” says Billy Goodman, managing director.
AFA Systems Ltd. supplies cartoners, case packers, and palletizers to snack and bakery producers. “Many snack food producers use our HD-LSP Heavy Duty Linear Servopack Autoload Cartoner,” says Eric Langen, sales and marketing director. “It can handle two lanes of incoming product to reduce the producer’s footprint and capital costs. Also, the system utilizes a simple collating system coupled with our gantry robot technology to ensure that multiple pack patterns and SKUs run on the same system.” The HD-LSP can reach speeds of 600 ppm and reduces reliance on manual labor.
Apex Motion Control offers robotic primary and secondary packaging configurations. The company recently helped a sweet bun producer solve a secondary packaging problem. “Our company integrated two Baker-Bots and an End of Line palletizing cobot that picks and places the finished packaged products into master boxes. The boxes are then sealed and moved to the end of the conveyor where our Baker-Bot 10 palletizing cobot places the boxes on pallets in predetermined formations,” says Jamie Bobyk, marketing manager.
The challenge was that the clamshells, product boxes, and finished master boxes were different sizes and weights. “The solution was quite simple in that end-of-arm soft grippers were used for both applications and parameters were set in the touch screen user interface. Now, the user can simply select which product from the touch screen and hit start,” Bobyk notes.
Wexxar Bel offers the TF100 and IPAK TF385 automatic tray formers for bakery and snack plants. The TF100 is a good entry-level solution for producers that want to add automation to their end-of-line operations. It has a servo-driven blank advance to form four-corner trays with accuracy, according to Mike Parkinson, product manager.
“During the last six months, we’ve been working with two bakeries that had automation in their primary and secondary lines but none in their end-of-line packaging,” Parkinson notes. “The TF100 proved to be a great solution for these companies because they were able to reduce labor in hand forming trays and distribute employees elsewhere to improve their packaging line without taking up a big footprint.”
A-B-C Packaging Machine Corp. manufactures end-of-line equipment: case erectors, packers, sealers, and palletizers for snack and bakery products, as well as depalletizers and partition inserters.
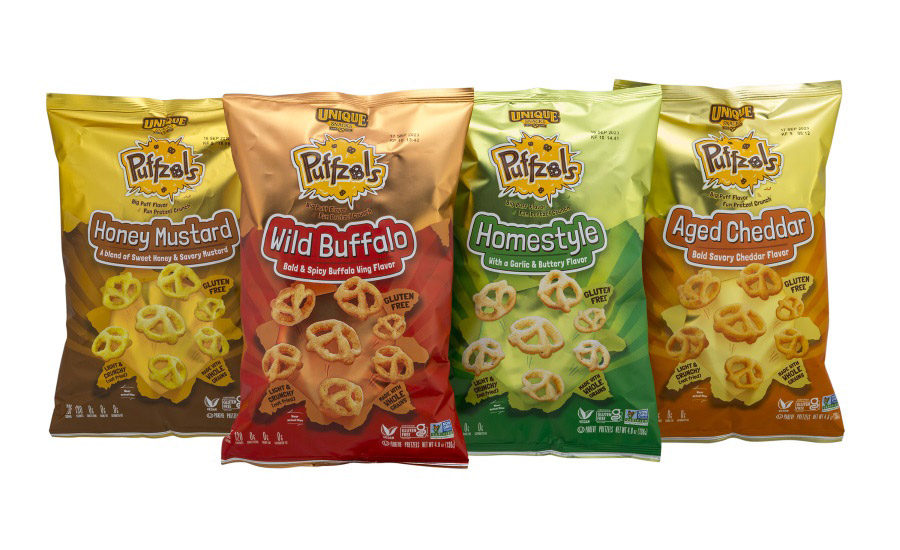
The company’s palletizers are used by snack and bakery producers to automatically accumulate and palletize cases of product, stacking them into squarely-formed pallet loads that maintain stability throughout transport. “We recently shipped a depalletizer to a snack producer that depalletizes both composite cans and plastic jars in multiple sizes to the packaging line,” says Bryan Sinicrope, vice president marketing and integrator sales. A-B-C’s equipment is designed for simple operation and control, so workers can quickly become proficient in managing the automated tasks.
Signode offers a wide range of automated packaging solutions for the bakery and snack market, a market that presents unique end-of-line packaging challenges due to varying product types, sizes, and material handling requirements, according to Rick Hantke, strategic marketing and customer insight director.
“One of our customers, a family-owned snack food operation, was struggling to keep up with rapidly growing product demand,” Hantke says. “Their case packing process was mostly manual, so forming, packing, sealing, and labeling each outgoing box by hand made it difficult to scale up production to meet demand.
To solve that problem, the snack producer added Signode’s Pack Point Complete Packaging Solution, which automates five job functions—forming, packing, sealing, printing, and labeling—in a single compact unit. “By automating these manual processes, the Pack Point system enabled the snack producer to improve efficiency and consistency across product lines, increase throughput, and realize significant annual cost savings,” Hantke adds.
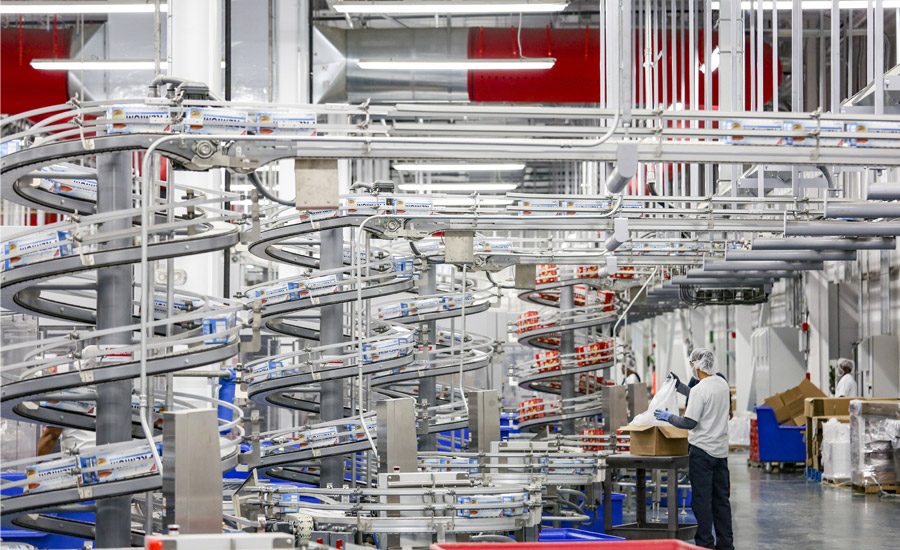
What advances lie ahead for automated packaging? Chan at Mondelēz International predicts the integration of sustainability, technological advances through automated ecosystems, and the ability to adapt to evolving consumer demands and regulatory standards. “These developments will lead to packaging solutions with a reduced ecological footprint and a comprehensive approach to end-to-end sustainability.”